forming processes sheet metal Forming of shallow parts using rubber tools. Maziar Ramezani, Zaidi M. Ripin, in Rubber-Pad Forming Processes, 2012. 4.1 Introduction. Sheet metal forming is a costly manufacturing process that is widely used in different industries. Many small companies are required to manufacture curved products and shallow parts with fine details in a small lot size which leads to both a . We’ve demonstrated fifteen fabulous cabinet colors that can go with black stainless steel appliances. Whether you choose a neutral shade like black, white, or gray, or you go with a dominant primary color like blue, red, or green, you have many color choices.Today's black stainless steel appliances are the chameleons of the kitchen—tthey're modern, polished, and current, and, if you want to design a kitchen that feels totally magazine-worthy, these are the best kitchen cabinet colors that go with black stainless .
0 · sheet metal working process pdf
1 · sheet metal stamping process pdf
2 · sheet metal processes pdf
3 · sheet metal forming process pdf
4 · sheet metal forming press dies
5 · sheet metal forming by hand
6 · sheet metal bending process pdf
7 · bulk deformation vs sheet metal forming
The yellow bit is the magnet, the grey metal bit is the ramp. The ramp is the bit that's hit first, so depending on which trains travel, depends on which end the ramp is on the magnet. If trains can travel both ways on the line in question, both ends will have a ramp.
sheet metal working process pdf
In this article, we’ll give you the lowdown on sheet metal forming, including the various processes, suitable materials, and its pros and cons. What is Sheet Metal Forming? Also known as sheet metal fabrication, sheet metal . Sheet metalworking, also known as Sheet metal forming and sheet metal fabrication, is a manufacturing process of cutting and forming relatively thin metal sheets, strips, and coils to create desired shape sheet .

large u metal enclosure
Metal forming processes Metal forming: Large set of manufacturing processes in which the material is deformed plastically to take the shape of the die geometry. The tools used for such deformation are called die, punch etc. depending on the type of process. Plastic deformation: Stresses beyond yield strength of the workpiece material is required.Numerical simulation of metal forming processes, as a component of the virtual manufacturing process, has a very important contribution to the reduction of the lead time. The nite element method is currently the most widely used .Forming of shallow parts using rubber tools. Maziar Ramezani, Zaidi M. Ripin, in Rubber-Pad Forming Processes, 2012. 4.1 Introduction. Sheet metal forming is a costly manufacturing process that is widely used in different industries. Many small companies are required to manufacture curved products and shallow parts with fine details in a small lot size which leads to both a .
The forming of the sheet can be carried out using mechanical tools, with air or with liquids, magnetically or with explosives. Special sheet metal processes include superplastic forming and press hardening, as well as the hot forming of aluminum and magnesium. Table 1 shows the common characteristics of sheet metal forming processes. The advent of CAD and CAM have unlocked laser cutting — a precise sheet metal forming process that directly influences a sheet’s size and silhouette. Fabricators favor laser methods for their granular control, speed, and compliance with pre-programmed cutting blueprints. For example, a laser cutter may follow schematic-based instructions to .
They are bulk forming processes and sheet metal forming processes. Each category includes several major classes of shaping operations. Bulk Deformation Processes: Bulk deformation processes are generally characterized by significant deformations and massive shape changes, and the surface area-to-volume of the work is relatively small. The term .Principles of Incremental Sheet Forming Incremental Sheet Forming is a versatile manufacturing process that involves the gradual deformation of a metal sheet using a localized tool. Unlike traditional forming processes that utilize dies and molds, ISF employs a CNC-controlled tool that moves incrementally, shaping the metal sheet layer by layer. Table 1: Materials used in sheet metal forming.. When selecting sheet metal materials for forming, the following factors are considered. Formability – Generally, materials with higher elongation percentage have better formability; Cost-effectiveness – Mostly, low-carbon steels are economical choice for general purposes.; Strength needs – AHSS and titanium .
Incremental sheet metal forming (ISMF) is commonly regarded as a die-less sheet metal forming process which can form complex three-dimensional parts using relatively simple tools. It is receiving attention from the engineering community due to its flexibility and low cost. This unique combination enables the rapid prototyping of functional .DOI: 10.1504/IJCAT.2012.046041 Corpus ID: 32943943; The optimal design of sheet metal forming processes: application to the clinching of thin sheets @article{Lebaal2012TheOD, title={The optimal design of sheet metal forming processes: application to the clinching of thin sheets}, author={Nadhir Lebaal and Marc Oudj{\`e}ne and S{\'e}bastien Roth}, journal={Int. J. . Giuliano G, Polini W. Influence of blank variable thickness on the material formability in hot gas sheet metal forming process. Manuf Lett 2020; 24: 72–76. Crossref. Google Scholar. 62. Kim YH, Lee J-M, Hong SS. Optimal design of superplastic forming processes. J Mater Proc Techn 2001; 112: 166–173. Crossref. The performances of the models are proved by the numerical simulation of various sheet metal forming processes: hydroforming, deep-drawing and forming of the complex parts. The book is useful for the students, doctoral fellows, researchers and engineers who are mainly interested in the mechanical modeling and numerical simulation of sheet metal .
#2. Sheet metal forming. Sheet metal forming involves the application of tensile and shears forces to fabricate sheets, plates, and strips to a desired possible shape using a set of tools. The punch and die are used as tools in the fabrication process.%PDF-1.4 %âãÏÓ 663 0 obj > endobj 685 0 obj >/Filter/FlateDecode/ID[704E8A5A77AA90E0E45753C1AAABDACC>]/Index[663 39]/Info 662 0 R/Length 112/Prev 3172114/Root 664 .86 8 Sheet Metal Forming Processes with the selection of stock width is done. This calls for several trial layouts. If A b represents the area of blanks produced in one press stroke and A s the strip area consumed by one press stoke or strip width times feed length, then theThe forming analysis system ARGUS supports the optimization of the sheet metal forming process. For the automatic optical forming analysis, sheet metal blanks are marked with a regular dot pattern with 1 mm, 2 mm or 3 mm distance in .
We would like to draw your attention to this Special Issue of JMMP on “Analysis and Modelling of Sheet Metal Forming Processes”. Analysis and modeling play a vital role for accessing the feasibility of sheet metal forming processes. Nowadays, almost no tool design in industrial stamping is manufactured without successful virtual tryout. 2. BULK DEFORMATION PROCESSES: Metal forming operations which cause significant shape change by deformation in metal parts whose initial form is bulk rather than sheet. These processes work by stressing metal sufficiently to cause plastic flow into desired shape. Performed as cold, warm, and hot working operations. In hot working, significant shape . Sheet metal forming process is carried out in the plane of the sheet by tensile forces with a high ratio of surface area to thickness. The high rate of production and formability is determined by its mechanical properties. Sheet metal components distributor use mechanical and hydraulic presses in manufacturing the sheet components.For more .
This practical and comprehensive reference gives the latest developments on the design of sheet forming operations, equipment, tooling, and process modeling. Individual chapters cover all major sheet forming processes such as blanking, bending, deep drawing, and more. The performances of the models are proved by the numerical simulation of various sheet metal forming processes: hydroforming, deep-drawing and forming of the complex parts. The book is useful for . Fine blanking Sheet Metal Forming Processes 34/7 8. MUHAMMAD TALHA NAWAZ (2K16-MET-15) 9. Shearing Dies Because the formability of a sheared part can be influenced by the quality of its sheared edges, clearance control is important. In practice, clearances usually range between 2% and 8% of the sheet’s thickness; generally, the thicker . The main sheet metal forming processes covered are tube bending and forming as well as bending of sheet and plate. Tube bending can be done via press bending, rotary drawing, heat induction, roll bending, and sand packing. Sheet and plate bending includes techniques like roll bending, air bending, bottoming, coining, folding, wiping, and rotary .
Sheet Metal Forming Processes. There are a variety of core manufacturing processes used to form sheet metal into parts. The techniques deployed depend on the geometries and production volumes needed, as well as the formability of the selected metal.Sheet-Metal Forming Processes TABLE 7.1 General characteristics of sheet-metal forming processes. Pr ocess Characteristics Roll forming Long parts with constant complex cross-sections; good surface Þni sh; high production rates; high tooling costs. Stretch form-ing Large parts with shallow contours; suitabl e for low-quan tity production ; high
sheet metal stamping process pdf
sheet metal processes pdf
large metal tool boxes
sheet metal forming process pdf
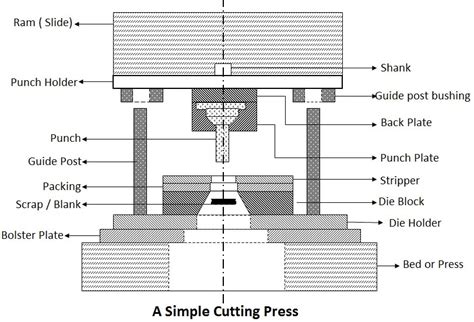
Here are some standard practices to follow to make your wiring installations look .
forming processes sheet metal|bulk deformation vs sheet metal forming