process planning sheet metal parts Sometimes it may be possible to combine two similar operations into one even though the shapes generated by the two operations are different. For example, features G and H . See more United CNC Machining is a leading manufacturer of prototype and CNC machined components.
0 · sheet metal process planning optimization
1 · sheet metal process planning
2 · sheet metal process
3 · sheet metal forming process
4 · sheet metal fabrication process
5 · sequence planning sheet metal parts
6 · progressive dies sheet metal sequencing
7 · progressive dies sheet metal
The Unicorn Oxford dartboard cabinet set features an official size 18" x 1.5" bristle board, ensuring authenticity for your gameplay. The rotatable metal number ring enhances .
Operations that give rise to features of the same type and have similar key parameters are said to be related. It is logical to perform these operations together at one station because they are very likely to have similar manufacturing requirements, e.g. . See moreThis criterion indicates where the feature occurs in the blank of the part. As suggested in , three different types of relations that characterise the location are suggested. They are: . See moreSometimes it may be possible to combine two similar operations into one even though the shapes generated by the two operations are different. For example, features G and H . See moreOne method to achieve positional accuracy of the die is to use pilot holes which are located either outside the part or are internal features. . See more
Table of Contents. 9 Steps in Sheet Metal Fabrication Process. Step #1: The Design Phase. Step #2: Material Selection. Step #3: Cutting the Metal. Step #4: Forming and Shaping. Step #5: .Process planning for sheet-metal press-brake forming involves the evaluation of: an optimum bending sequence with suitable gauging strategy, tooling requirement, and individual punch displacements [3]. . Algorithms for the design verification and automatic process planning for bent sheet metal parts. CIRP Ann Manuf Technol 48(1):405–408 .
3D vision inspection of sheet metal parts is usually a time-consuming task and hence not suitable for real-time measurement of 3D geometric features.To address this problem, this work presents an .The integration of computer‑aided design (CAD), computer‑aided process planning (CAPP), and . parts for metalworking, with scarce attention given to sheet metal parts, another widely used .
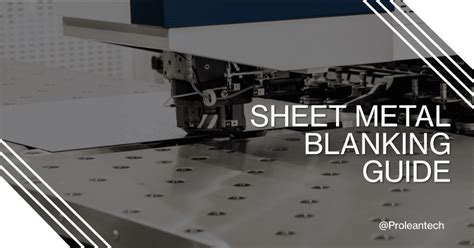
Sheet-metal parts are conventionally used to replace expensive cast and forged products in mass production in the automotive industries. Sheet-metal stamping to produce parts with freeform . To facilitate process planning, a new sheet-metal part is analyzed to indentify fundamental features in the form of an attributed graph. The new case . This paper describes an expert system developed for process planning of sheet metal parts produced on compound die. The proposed system is organized in six modules.The production rule based expert . The development of an expert system for both process planning and die design of sheet metal cutting and piercing operations is described, which can be used by both the designer deciding on the production feasibility (manufacturability) for a sheet metal component and by the manufacturer receiving advice either on the hardware needed or on the process plan.
Manufacturability assessment and process planning of sheet metal parts are important activities for the design of a compound die. This paper describes the research work involved in the development . The integration of computer-aided design (CAD), computer-aided process planning (CAPP), and computer-aided manufacturing (CAM) systems is significantly enhanced by employing deep learning-based .Ever wondered what goes into shaping the metal components we use daily? The answer lies in the meticulous sheet metal fabrication process. Understanding this process is crucial for businesses and professionals in the metal industry. The sheet metal fabrication process is an intricate journey from raw metal to a finished product. It involves .
Process planning of sheet metal part is an important activity in the design of compound die. Traditional methods of carrying out this task are manual, tedious, time-consuming, error-prone and experience-based. This paper describes the research work involved in the development of an expert system for process planning of sheet metal parts produced on . Sheet metal bending, an essential part of manufacturing, is increasingly used in transportation, aerospace, and related fields. Challenges related to forming accuracy and path generation have always been major concerns in industrial applications. A prediction model based on GA-BPNN (Genetic Algorithm-Backpropagation Neural Network) was developed, .

integration with computer-aided process planning (CAPP) aspect. 2. Sheet Metal Forming Processes Common sheet metal fabrication techniques include a multitude of different operations. These operations can be classified as in Table 2. Bending and punching are the most popular sheet metal forming processes. Some operations, such as folding,
There are different tools to manufacture sheet metal parts, including (CNC) press brakes, laser cutting and dies. Some of the smaller sheet metal parts required in large quantities are usually made using progressive dies because the process is stable, has high productivity and is . Sheet metal parts have been widely used in industry and much information for parts has been accumulated in the database. In planning the manufacturing process of a sheet metal part, if the similar .2.4 Process Planning for Parts 2.5 Route Sheet or Operation Sheet 2.6 Process Planning for Assemblies 2.7 Process Planning Economics 2.8 Make or Buy Decision . The basic processes includes metal casting, forging and sheet metal rolling. In the basic process, it establishes the initial geometry of the part. Secondary Processes . 16
sheet metal process planning optimization
Sheet metal bending is a major manufacturing process to transform sheet metal blanks into complex 3D parts. It is recognized but still the state of the art in CNC sheet metal bending is still .
2. Guidelines for process planning of sheet metal parts produced on compound die From the critical review of published literature and detailed discussions with experienced die designers, some basic guidelines for process planning of sheet metal parts pro-duced on compound die are identified [1, 9, 10, 14–18]. A Process Planning for Sheet Metal A number of systems have been developed to automate some aspects of the macro planning problem for sheet metal parts.~9-22 These systems attempt to handle a wide variety of sheet metal processes and attempt to order various operations based on high-level interac- tions among them.design and manufacturing process planning of discrete sheet metal parts. Following is the procedure of vendor neutral design and manufacturing of discreet sheet metal parts : 6. Identification of total number of flat faces along with exact dimensions. 7. Arrangement of flat faces and the connecting bends characteristics. 8.
C.-H. Wang, D.A. Bourne, Using features and their constraints to aid process planning of sheet metal parts, in: Proceedings of the IEEE International Conference on Robotics and Automation, vol. 1, May 1995, pp. 1020–1026. Dr. Joost R. Duflou holds master degree in architectural engineering and in electro-mechanical engineering. He obtained a .
Sheet metal manufacturing is the process of creating sheet metal parts by cutting, bending, and forming thin metal sheets into specific shapes and sizes. The process typically uses coating, cutting, bending, and assembly techniques. Sheet metal is made from various materials, including steel, aluminum, zinc, and copper. This paper describes an expert system for die design and process planning of sheet metal forming operations functioning on a part representation by custom-defined features input incrementally . Process planning for sheet metal bending parts refers to the sequential order of the bending processes during fabrication. The bending sequence should be arranged based on the shape of the part, precision requirements, nature of the operations, and the pattern of material deformation. . The bending process plan mainly includes process .For sheet metal parts with a large number of bends and a complex structure, the randomness in the selection of the initial population is too strong, and the appropriate value is generally too large, which makes the selection of the initial population too large. . Using the improved genetic algorithm to carry out process planning for sheet .
Part representation and feature classification methods for bent sheet metal parts are also discussed. Sections are dedicated to the core problems of fully automated process planning in sheet metal bending: bend sequencing, collision detection, tolerance verification and tool . Instead, place the part closer to the work clamps or even in the middle of the sheet to prevent sheet distortion and improve results. Also, keep in mind the direction in which the wheel tool will operate. If the tool moves toward the work clamps, the risk of sheet buckling increases. Instead, have the sheet move away from the clamps.
Progressive dies are widely used for the mass manufacture of sheet metal parts requiring several stamping operations. Sequencing these stamping operations is vital as it influences the design of .
sheet metal process planning

Bronze Underwater Junction Boxes for Fountain Lighting. Connect multiple fountain lights to a single power supply with these bronze junction boxes; Available in two sizes - four or eight outlet; Available without a bottom inlet or with 1" FTP bottom inlet; Once installed fill with junction box potting compound (sold separately)
process planning sheet metal parts|sheet metal forming process