weld sheet metal to steel Each welding process requires specific precautions and equipment setup for a successful sheet metal weld. So, let’s discuss the preparation needed for each arc welding process before proceeding to the common problems with thin gauge welds. See more The actual electricity box can be painted with either acrylic paint or spray paint. On a similar note, you need to make sure that your gas reader is still readable. In other words, you can paint the exterior, but you cannot paint over the glass (or see-through plastic).
0 · welding holes in sheet metal
1 · welding 24 gauge sheet metal
2 · welding 22 gauge sheet metal
3 · welding 20 gauge sheet metal
4 · welding 16 gauge sheet metal
5 · welding 14 gauge sheet metal
6 · welder settings for sheet metal
7 · mig welding sheet metal basics
A junction box is used to add a spur or to extend circuits and direct power to lights and additional sockets. Advice on wiring electrical junction box with easy to follow junction box wiring diagrams, including information on 20 and 30 amp junction .
Each welding process requires specific precautions and equipment setup for a successful sheet metal weld. So, let’s discuss the preparation needed for each arc welding process before proceeding to the common problems with thin gauge welds. See more
Now that we’ve covered the essential considerations for different arc welding processes, let’s discuss how to prevent and fix common . See moreWelding thin metal is challenging. There is no denying that. But, if you practice and use the tips we shared in this article, you’ll get the best chance for success. After you inevitably burn through some scrap sheets of metal and warp others, you’ll gain more experience and learn . See more Preventing burn-through and warping when welding sheet metal is all about controlling the heat. Choose the right welding process and filler metal, and follow these . Stick welding of sheet metal shall be carried out using AWS A5.1/A5.1M E6013 (CWB/CSA W48-06 E4313) type electrode of diameter 5/64 inch or 2.0 mm. E6013 types electrode offer very good arc stability, easy-to .
Welding thin sheet metal can be challenging because you need to obtain adequate fusion while preventing distortion and burnthrough. The key skill is to control the heat across the sheet metal to prevent defects. This guide .
welding holes in sheet metal
welding 24 gauge sheet metal
To braze weld sheet metal, first, clean the metal surfaces, apply flux, heat the metal, and then apply the brazing rod. Braze welding can be done with a . Sheet metal comes in different types such as stainless steel, .Most of the light gauge sheet metal work will require the use of .023- or .24- inch while if you have a sheet metal having a gauge of more than 18-gauge then a .030-inch wire would be the most ideal. A ER70S-6 wire would be most ideal . Welding thin metal doesn't have to cause a headache! We've put together this relatively easy step-by-step guide to help you get started on your next thin metal weld. . that are slimmer as compared to reedy sheet metal. Numerous welders utilize 0.023-inch diameter wires and 0.024 inches for slimmer sheet metals. 18-gauge metals such as . Can You Weld 22-Gauge Sheet Metal? You can weld a 22-gauge (0.03-inches) metal sheet using a TIG welder or even with a MIG welding unit. However, it is not recommended to stick weld 22-gauge sheet metal as excessive penetration is highly likely to occur and become problematic. The 16 gauge or 1.5mm is a safe bottom limit for material thickness .
If you are welding sheet metal, make sure the equipment you are using is designed for welding sheet metal. You should also make sure that the position you are welding from is clear of other metal parts. Summary of How To Weld Sheet Metal On A Car. Wet welding is the process of sticking metal components together with melted metal. Find below the MIG Welding Sheet Metal Settings Chart which displays the recommended settings for welding different gauge thicknesses of sheet metal. To ensure optimal results, select the appropriate gauge thickness and refer to the corresponding joint gap, wire diameter, amperage, and voltage setting for your weld. Get the J-B Weld glue for metal at Amazon, The Home Depot, Grainger, or J-B Weld. . Setting and curing times: Sets in 5 minutes and is steel hard in 15 minutes; fully cures in 1 hour;
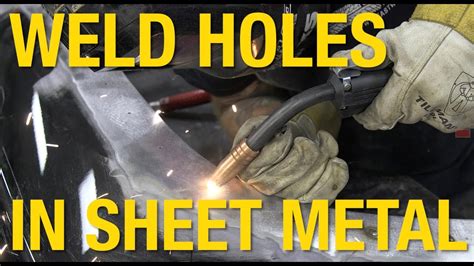
Preparing the Sheet Metal for Plug Welding Sheet Metal. Before initiating the plug welding sheet metal process, it’s imperative to prepare the sheet metal to ensure optimal weld quality and structural integrity. The following steps outline the essential preparations for achieving successful plug welds: Thin to thick, here's the trick!Learn faster with an online welding course: https://courses.timwelds.comOther Helpful Videos: MIG Welding Settings: https://y.
welding 22 gauge sheet metal
Spot welding is a great way to join two pieces of sheet metal together quickly and easily. With the right equipment and technique, anyone can learn how to spot weld quickly and efficiently! Remember to wear proper safety gear when working with electricity or hot metals—your safety should always be your top priority when tackling any new project! The brazing alloy has a much lower melting point than steel, so you need to heat the pieces to a lower temperature than you would when welding. To get to the right temperature for brazing, which is usually 800–2,000 degrees Fahrenheit depending on the alloy, you can use equipment that is not as powerful as a welding machine, including propane .
Gas welding sheet metal is a great way to join two pieces together quickly and efficiently without having to rely on traditional methods such as soldering or brazing. With the right tools and know-how, however, anyone can become a master at gas welding sheet metal in no time! . How to Gas Weld Mild Steel – A Complete Guide. Similar Posts . A: Thinner rods such as the 6010 or 6011 are typically required for sheet metal welding. These rods are effective in low amp and facilitate good control which is very important especially when welding the very thin materials to avoid burn through. Q: Is it possible to weld thin sheet metal with a Lincoln stick welder that has seen better days? Hey everyone, I've got 62!! 3/8" holes to weld up on my fenders,doors and quarterpanels after removing all the stainless trim. I recall seeing an article in Street Rodder a few years ago about a supplier for weld in mild steel plugs in a few common sizes. Any ideas on where I might find them? The thought of scribing/cutting that many gives me . #welddotcomWe are still working through your requests that were submitted through our Instagram story. @bostonrush77 asked us to show how to do old rusty she.
cnc precision machining exporter
If you want to go the cheapest route possible, JB Weld does make a 5 minute quick setting epoxy that I've had decent luck with on metal and plastic. No matter what you decide to use, leave the area where the hole is low enough that you . Welding autobody panels. Auto body sheet metal is relatively thin, and this can present some challenges for welders particularly those who are accustomed to welding thicker materials. Welding nearly always causes some distortion: the metal in and around the weld shrinks as it cools, and this shrinking often upsets the shape of the metal . To weld sheet metal you need a tig or mig with the gas bottle. These to welder you can weld at lower temps. . needed when welding thin stock..Very seldom is one going to be able to use a continous weld like we use in structrual steel when welding thin body metal with any kind of equipment.. Sam . Induction welding; Welding Sheet Metal. For welding purposes, the term “sheet metal” is restricted to thicknesses of metals up to and including 1/8 in. (3.2 mm). Welds in sheet metal up to 1/16 in. (1.6 mm) thick can be made satisfactorily by flanging the edges at the joint. The flanges must be at least equal to the thickness of the metal.
How To Weld Sheet Metal The RIGHT WAY - SUPER EASY#howto #diy #welding My Friend Pete shows us the easiest and simplest way to weld sheet metal. From butt w. Welding sheet metal with a stick welder is a bit more challenging, especially when welding thin sheets of metal. The heat input in stick welding is generally . E6011 is commonly used as an all purpose electrode for automobile body shops and mild steel farm equipment. Other uses would include shipbuilding, bridges, boilers, barges, railroad . Welding sheet metal can be difficult. This 2 part video explains & demonstrates the basic techniques and tips for first time sheet metal welders. LINK TO BUY.
New to the forum and I am a hobby welder. I have a HF Flux 125 that I converted to DCEN with a rectifier and 90,000mfd of capacitance to smooth it out. Noticed a huge difference in quality vs AC like the welder came. Much better "sizzle", less spatter etc. I had always been using the wire that came with the machine but read about that wire sucking. The Hobart Handler 140 is an excellent choice for sheet metal welding due to its versatility and user-friendliness. With an amperage range of 25 to 140A, it’s capable of handling various thin materials, including sheet metal. . Whether you’re welding thin carbon steel or folding sheet metal into intricate shapes, it’s essential to .
Acrux7 16 PCS Butt Welding Clamps, Small Sheet Metal Clamp, Carbon Steel Panel Clamps for Auto Body Edge to Edge Welding (1x2.3 Inch) 4.6 out of 5 stars. 11. . QWORK 10" Nickel Plated High Carbon Steel Locking Sheet Metal Clamp, 2-Pack with Trigger Release and Adjustable Mechanism for Metalworking, Adjustable Opening Nickle Plated Welding Plier. Use thin wire-One big mistake we see with beginners is using welding wire that is too thick for the metal they’re welding. If your welding wire is too thick it will take more heat to melt the wire than the substrate and can make it even more prone to blowing holes in the panel. For thinner gauge sheet metal like 18 or 20 gauge we suggest .023 .

welding 20 gauge sheet metal
The 1/16" easy strike and Lincoln 6013 are the only option for stick welding sheet metal. make very short tack welds and space them out so you don't blow trough the metal. You can also easily warp the metal if you don't tack it up first. I make small 1/4" long tacks and tie them together gradually.
weld sheet metal to steel|welding holes in sheet metal