sheet metal forming analysis This unique textbook features fundamentals and analyses of metal forming processes supported by 200 worked numerical examples. It provides rigorous detail on the three all-important groups of metal-forming processes: bulk-metal . CNC stands for Computer Numerical Control, which refers to the computerized operation of machining tools used in manufacturing. CNC machines operate using pre-programmed software and codes, which tell each machine the .
0 · sheet metal forming tools
1 · sheet metal forming
Yes, multiple circuits may exist in a junction box. Durango, CO, 10 h 20 min from the winged horses. Can a dual (or larger) gang box have two different circuits feed it? Not necessarily a MWBC, just two different circuits.
Forming analysis is a process to evaluate the forming states and surface strain levels of sheet metal components after press forming. Before forming, the raw sheet metal blanks are marked using electro-chemical etching or laser .It illustrates several different approaches to this intricate field by taking the reader through the hows and whys of product analysis, as well as the techniques for blanking, punching, bending, .For sheet metal forming analysis within the metal forming process, a successful technique requires a non-contact optical 3D deformation measuring system. The system analyzes, calculates and documents deformations of sheet metal parts, for example. It provides the 3D coordinates of the component's surface as well as the distribution of major and minor strain on the surface and the material thickness reduction. In the Forming Limit Diagram, the measured deformations are com.
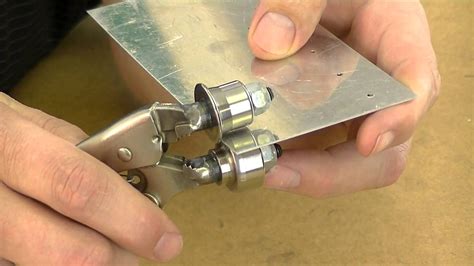
Ansys Forming is an all-in-one forming simulation software built to digitally design and validate every step of the sheet metal forming process with speed and accuracy. Learn More. Validate .
This unique textbook features fundamentals and analyses of metal forming processes supported by 200 worked numerical examples. It provides rigorous detail on the three all-important groups of metal-forming processes: bulk-metal . Analysis and Optimization of Sheet Metal Forming Processes comprehensively covers sheet metal forming, from choosing materials, tools and the forming method to optimising the entire process through finite element .
In this chapter, sheet-metal formability tests, such as the tensile test, the plane-strain test, and the in-plane stretching test are analyzed.
Using finite element analysis (FEA), the sheet metal-forming process and the influence of various process parameters on formability can be studied. In the present work, the raw material size is optimized with the help of FEA analysis. Inputs required to simulate a sheet metal-forming process are computer-aided design (CAD) model of the forming .detailed formability analysis in GM’s production developments. Targeting the requirements of feasibility and formability analyses, the key techniques of using LS-DYNA® in sheet metal forming simulations are systematically studied, such as element formulation, material model, adaptive meshing, and mass scaling, etc. The study shows that the .Abstract : Sheet metal forming is a process that is now widely utilised in the automotive and aerospace sectors. The forming process is an old industrial technique in which metal is . is used for CAD modelling and finite element analysis (ANSYS design Modeler). For the material, graphs of Equivalent Stress (Von-misses Stress), Total .
We would like to draw your attention to this Special Issue of JMMP on “Analysis and Modelling of Sheet Metal Forming Processes”. Analysis and modeling play a vital role for accessing the feasibility of sheet metal forming processes. Nowadays, almost no tool design in industrial stamping is manufactured without successful virtual tryout.It provides rigorous detail on the three all-important groups of metal-forming processes: bulk-metal forming, sheet-metal forming, and sheet-bulk-metal forming. Theory of metal forming is presented by discussing deformation behavior, plasticity, and formability with a thorough mathematical analyses and calculations. Aluminum alloy materials have been widely used in automobile, aerospace and other fields because of their low density, high specific strength and corrosion resistance. The process of the warm forming of aluminum alloy improves the formability of aluminum alloy sheets, reduces the deformation resistance and spring-back and improves the forming accuracy and .
This paper presents a methodology that allows for the detection of the state of a sheet-metal-forming press, the parts being produced, their cadence, and the energy demand for each unit produced. For this purpose, only electrical measurements are used. The proposed analysis is conducted at the level of the press subsystems: main motor, transfer module, . 1. Mathematical background 2. Introduction to the finite element method 3. Finite elements for large deformation 4. Typical finite elements 5. Classification of finite element formulations 6. Auxiliary equations: contact, friction, incompressibility 7. Thermo-mechanical principles 8. Sheet metal formability tests 9. Steady state forming problems 10. Forging . Under a boundary lubrication regime, the effect of sliding velocity and normal loads on the friction coefficient in the sheet metal stamping process was investigated using a pin-on-disk sliding wear test. Software was used to analyze both the data generated and the friction coefficient; in addition, a variable friction model based on different velocities and normal loads .
Finite element analyses and simulations of sheet metal forming processes. Engineering Computations, Vol. 21, Issue. 8, p. . Metal Forming Analysis, first published in 2001, describes the most important numerical techniques for simulating metal forming operations. The first part of the book describes principles and procedures and includes . Analysis and Optimization of Sheet Metal Forming Processes comprehensively covers sheet metal forming, from choosing materials, tools and the forming method to optimising the entire process through finite element analysis and computer-aided engineering.. Beginning with an introduction to sheet metal forming, the book provides a guide to the various .
10th International LS-DYNA® Users Conference Metal Forming (1) 2-27 Sheet Metal Forming Simulation and Real World Tooling Matt Clarke Continental Tool and Die Windsor, CA [email protected] . Analysis the aforementioned problems, it is identified that the of the binder was flexing. In the area of the pad, where it had the least .Request PDF | On Jan 1, 2002, Ch. Klimmek and others published Finite element analysis of sheet metal forming by spinning | Find, read and cite all the research you need on ResearchGateof sheet metal forming analysis and, also, to determine directions of future research to advance technology that would be useful in metal stamping plants. Metal deformation analyses which provide guide lines for metal flanging are already in use. Theories, Methods and Numerical Technology of Sheet Metal Cold and Hot Forming: Analysis, Simulation and Engineering Applications (Springer Series in Advanced Manufacturing) 2013th Edition . by Ping Hu (Author), Ning Ma (Author), Li-zhong Liu (Author), & 5.0 5.0 out of 5 stars 2 ratings. Part of: Springer Series in Advanced Manufacturing (71 .
With the increasing need from industries, there have been remarkable advances in the sheet metal forming analysis by the finite element method [1], [2], [3], [4].In order to save the time and the effort in the product and process design, the finite element approach is indispensable for accurate sheet metal forming analysis. INTRODUCTION Sheet metal forming analysis by the finite element method has gained general popularity with a burst of development in finite element techniques [1-5]. Since a sheet metal forming process experiences large deformation and rotation due to stretching and bending into a very complicated shape, a finite element approach is .In some sheet metal forming processes, there is no need for the holder and this is known as air bending such as V-bending and U-drawing as shown in Figure 1. . analysis for sheet metal bending are in close agreement with experimental results. Jaisinghet. al.[6] .
Modern software programs are routinely used by industries to study the characteristics of and to reduce the cost of sheet metal parts that are used in automotive and other applications. Virtual simulations that are based on complex math models and state-of-the-art computational tools play a very important role in reducing the high costs associated with . The forming of complex sheet metal parts is expensive and requires energy-intensive inputs. The sheet parts are typically made from steel or aluminum, and production of these two metals accounts for over 10% of global anthropogenic carbon dioxide emissions (Allwood et al., 2012).Work by Cullen et al. (2012) and Cullen and Allwood (2013) suggests . Sheet metal forming is a very important process in industry to create a wide variety of goods. The analysis of local ductility and residual stresses is important both to assess the viability of the manufacturing process and the reliability of the resulting elements in service.
T1 - Measuring and modeling friction for sheet metal forming process analysis and control. AU - Hao, Shanlin. AU - Ramalingam, Subbiah. AU - Klamecki, Barney E. PY - 1995/12/1. Y1 - 1995/12/1. N2 - Results of work describing several aspects of specifying and using friction for design and control of sheet metal forming processes are presented. The sheet metal forming process is a unique type of metal forming process which enables the deformation of metals that are less than 6mm in thickness. In our analysis, we considered three different materials i.e.Aluminium, Stainless steel and Carbon steel-1020- annealed, that undergoes Bending stress using V die. The analysis is carried out using Finite .
The formation of sheet metal products is now widely utilized for multi-purposes in the automotive, aerospace and in industrial sectors. In this study, the phenomenon of plastic strain, von Mises stress, shear train by the V-bending method and to analyze the results theoretically, by using a special program called ANSYS. The multi-layer sheet metal in the .This chapter provides an introduction to metal forming processes and where they fit among the five general areas of manufacturing. It also discusses the basic differences between bulk deformation and sheet-metal forming processes and how they relate to hybrid forming processes such as drawing, bending, and coining.Sheet metal forming is one of the most commonly used processes in industry. Throughout the years, the sheet metal forming industry experienced technological advances that allowed the production of complex parts. However, the advances in die design progressed at . The analysis is done both numerically and analytically/manually. Numerical Analysis is done using ANSYS and LS-DYNA. The influence of sheet metal thickness, sheet metal type, friction, tool radius and tool shape on spring back for Aluminium, copper, mild steel and High strength steels, sheet metal have been considered for investigations.
sheet metal forming tools
sheet metal forming
GAUGE TO THICKNESS CHART Gauge Stainless Galvanized Sheet Steel Aluminum Fraction inches (mm) inches (mm) inches (mm) inches (mm) . 13 3/32 0.094 (2.4) 0.0934 (2.37) 0.0897 (2.28) 0.072 (1.8) . 3/16” & thicker is plate SHEET .
sheet metal forming analysis|sheet metal forming tools