anti foam for cnc machining Foaming in CNC machining coolant systems is a common issue that can lead to decreased efficiency, poor surface finishes, and even potential damage to the machinery. Understanding the causes of foaming and implementing effective solutions can help maintain a . So here are 11 ways to prevent sheet metal from warping in TIG welding. Make light passes; Use intermittent welding; Use backstep welding; Limit the number of passes; Weld along the neutral axis; Anticipate shrinkage; Move around on your project; Use clamps to control expansion; Fix problems before they permanently set; Work quickly
0 · hobby cnc foam cutter
1 · high density foam cnc
2 · cnc router for foam cutting
3 · cnc machine for foam cutting
4 · cnc machine for eva foam
5 · cnc foam router for sale
6 · cnc foam machining services
7 · best router bit for foam
Heavy-duty welded steel construction for strength and durability; Shelves are fully adjustable on 2” centers to accommodate a variety of storage items; Shelves hold up to 200 - 230 lbs of evenly distributed weight; Recessed handle with 3-point locking system for added security; Chip- and corrosion-resistant powder-coated finish for lasting .
Foaming in CNC machining coolant systems is a common issue that can lead to decreased efficiency, poor surface finishes, and even potential damage to the machinery. Understanding the causes of foaming and implementing effective solutions can help maintain a .Foaming in CNC coolant systems can significantly hinder machining .Continuous monitoring and maintenance are crucial for preventing coolant .Choosing the right coolant is essential for maintaining the efficiency and .
Foaming in CNC coolant systems can significantly hinder machining performance and efficiency. By using anti-foaming additives specifically designed for CNC coolants, you can .
Continuous monitoring and maintenance are crucial for preventing coolant foaming in CNC machining operations. Foam can significantly reduce the effectiveness of the coolant, . What you can do is to try to eliminate the things that excite the coolant and add unwanted air to the coolant. Limiting coolant flow and pressure to what is needed is a good .
non metallic light fixture box
With most coolants that I've worked with you can go about as low as 5 without any problems. Also, you should be able to get some anti-foam from you chemical supplier, seem .
Ever dealt with annoying coolant foam? Let's talk about how water hardness plays into it, and learn about how to tackle this issue and keep your machining foam-free. Coolant foaming during metalcutting can be a messy headache. But with a little detective work, this bubbly problem may be understood and controlled. Foaming in CNC machining coolant systems is a common issue that can lead to decreased efficiency, poor surface finishes, and even potential damage to the machinery. Understanding the causes of foaming and implementing effective solutions can help maintain a smooth and efficient machining process.
Foaming in CNC coolant systems can significantly hinder machining performance and efficiency. By using anti-foaming additives specifically designed for CNC coolants, you can effectively break down foam and prevent its formation.
Continuous monitoring and maintenance are crucial for preventing coolant foaming in CNC machining operations. Foam can significantly reduce the effectiveness of the coolant, leading to overheating, increased tool wear, and compromised machining quality. What you can do is to try to eliminate the things that excite the coolant and add unwanted air to the coolant. Limiting coolant flow and pressure to what is needed is a good place to start. The cabinet washdown-flood system is also another place to look. Often, the washdown is not needed on a continuous basis. With most coolants that I've worked with you can go about as low as 5 without any problems. Also, you should be able to get some anti-foam from you chemical supplier, seem as though all coolant manufacturers make an anti-foam for their product. Ever dealt with annoying coolant foam? Let's talk about how water hardness plays into it, and learn about how to tackle this issue and keep your machining foam-free.
Coolant foaming during metalcutting can be a messy headache. But with a little detective work, this bubbly problem may be understood and controlled. If you aren't using high pressure coolant pumps and you are getting foaming, you should be getting free support (and defoamer) from your coolant supplier. And, and explanation of why their product is failing. First, let's back up. The No.1 common cause of foaming is HP applications with coolants not intended to be used for HP.
Shop quality Coolant Additives Treatments Test Strips at MSC Direct today! Our premium selection features lasting durability and top performance. Choosing the right coolant is essential for maintaining the efficiency and performance of your CNC machining operations. By consulting with your coolant supplier and selecting a coolant with anti-foaming properties, you can prevent foaming, enhance lubrication, and improve machining performance. Foaming in CNC machining coolant systems is a common issue that can lead to decreased efficiency, poor surface finishes, and even potential damage to the machinery. Understanding the causes of foaming and implementing effective solutions can help maintain a smooth and efficient machining process. Foaming in CNC coolant systems can significantly hinder machining performance and efficiency. By using anti-foaming additives specifically designed for CNC coolants, you can effectively break down foam and prevent its formation.
Continuous monitoring and maintenance are crucial for preventing coolant foaming in CNC machining operations. Foam can significantly reduce the effectiveness of the coolant, leading to overheating, increased tool wear, and compromised machining quality. What you can do is to try to eliminate the things that excite the coolant and add unwanted air to the coolant. Limiting coolant flow and pressure to what is needed is a good place to start. The cabinet washdown-flood system is also another place to look. Often, the washdown is not needed on a continuous basis. With most coolants that I've worked with you can go about as low as 5 without any problems. Also, you should be able to get some anti-foam from you chemical supplier, seem as though all coolant manufacturers make an anti-foam for their product.
non-metallic receptacle box
Ever dealt with annoying coolant foam? Let's talk about how water hardness plays into it, and learn about how to tackle this issue and keep your machining foam-free.
Coolant foaming during metalcutting can be a messy headache. But with a little detective work, this bubbly problem may be understood and controlled.
If you aren't using high pressure coolant pumps and you are getting foaming, you should be getting free support (and defoamer) from your coolant supplier. And, and explanation of why their product is failing. First, let's back up. The No.1 common cause of foaming is HP applications with coolants not intended to be used for HP.Shop quality Coolant Additives Treatments Test Strips at MSC Direct today! Our premium selection features lasting durability and top performance.
non metallic enclosure box
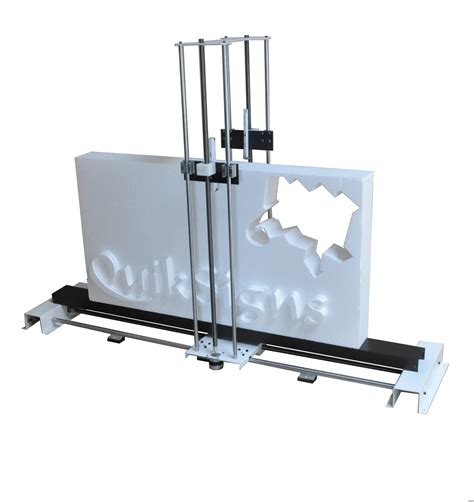
hobby cnc foam cutter
Welders bring their welding skills and knowledge, while fabricators contribute their expertise in metal shaping, cutting, and assembly. Together, they create a more comprehensive skill set within the team.
anti foam for cnc machining|best router bit for foam