metal sheet forming process #2. Sheet metal forming. Sheet metal forming involves the application of tensile and shears forces to fabricate sheets, plates, and strips to a desired possible shape using a set of tools. The punch and die are used as . Find Chicken House Trusses in For Sale. New listings: 32Steel trusses/reclaimed chicken house material $1.
0 · sheet metal working process pdf
1 · sheet metal stamping process pdf
2 · sheet metal processes pdf
3 · sheet metal operations with diagrams
4 · sheet metal forming process pdf
5 · sheet metal bending process pdf
6 · forming sheet metal by hand
7 · bulk deformation vs sheet metal forming
HOLZ-HER EVOLUTION 7405 4MAT: The EVOLUTION 7405 4mat Vertical CNC Drilling and Machining Center offers complete CNC machining in a compact format. The EVOLUTION series offers unique patent-pending solutions for .
In this article, we’ll give you the lowdown on sheet metal forming, including the various processes, suitable materials, and its pros and cons. What is Sheet Metal Forming? Also known as sheet metal fabrication, sheet metal .Chap 2 , sheet metal – p. 1 Sheet Metal Forming Processes • involves workpieces with a high ratio of surface area to thickness • plates, thickness > ¼ inch • sheets, thickness ≤ ¼ inch • typical items produced by sheet-metal forming processes: metal desks appliance bodies . hubcaps aircraft panels . beverage cans car bodies
Sheet metalworking, also known as Sheet metal forming and sheet metal fabrication, is a manufacturing process of cutting and forming relatively thin metal sheets, strips, and coils to create desired shape sheet . #2. Sheet metal forming. Sheet metal forming involves the application of tensile and shears forces to fabricate sheets, plates, and strips to a desired possible shape using a set of tools. The punch and die are used as .Sheet metal expanding is a specialized process within sheet metal forming that involves stretching the metal to create a mesh-like pattern. This technique enhances the flexibility and strength of the sheet metal, making it suitable for various applications, including filtration, screening, and architectural details.
Coming to the sheet metal forming processes itself, drawing and bending are the two most widely used techniques in sheet metal industry. Both experimental and FE based simulation works have been done in analyzing these two processes. It is understood from the literature that punch nose radius and die shoulder radius coupled with appropriate . Since the 1960s, numerical simulation has replicated the sheet metal forming process. The utilization of numerical simulation has grown progressively in examining intricate engineering obstacles. Researchers are investigating numerical analysis methods to address various problems associated with the sheet metal forming process. Sheet Metal Forming Processes; Power metal forming process; Bulk Forming Processes. Bulk forming process involves using raw materials with a low surface area to volume ratio for shaping. This category includes processes like rolling, forging, extrusion, and drawing. Different forces, such as compressive, tensile, shear, or a combination of .Forming of shallow parts using rubber tools. Maziar Ramezani, Zaidi M. Ripin, in Rubber-Pad Forming Processes, 2012. 4.1 Introduction. Sheet metal forming is a costly manufacturing process that is widely used in different industries. Many small companies are required to manufacture curved products and shallow parts with fine details in a small lot size which leads to both a .
The forming limit analysis proceeded during the sheet metal forming process at various elevated temperature. The fracture’s forming load, stroke, and position were determined for different . Giuliano G, Polini W. Influence of blank variable thickness on the material formability in hot gas sheet metal forming process. Manuf Lett 2020; 24: 72–76. Crossref. Google Scholar. 62. Kim YH, Lee J-M, Hong SS. Optimal design of superplastic forming processes. J Mater Proc Techn 2001; 112: 166–173. Crossref.
Stamping is a fundamental sheet metal forming process widely employed in manufacturing industries such as automotive and appliances. This process involves shaping metal sheets into desired forms and configurations using specialized dies and punches. The metal sheet is placed between the dies, and pressure is applied to deform the material . A hybrid incremental sheet forming experimental platform was designed (Fig. 1). During the forming process, the sheet is clamped by a support die and a blanker holder, and the change of forming forces is monitored by a dynamometer. The principle of a hybrid incremental sheet forming is shown in Fig. 1a. Through the dual incremental compression .Metal forming processes Metal forming: Large set of manufacturing processes in which the material is deformed plastically to take the shape of the die geometry. The tools used for such deformation are called die, punch etc. depending on the type of process. Plastic deformation: Stresses beyond yield strength of the workpiece material is required.
In this forming process, sheet metal parts are formed by a smooth-end tool in a stepwise way, during which plastic deformation is highly localized around the tool end. The part geometric accuracy .After the precise cutting of metal sheets, the subsequent stage in sheet metal fabrication is the forming and shaping process. This phase is essential for giving the flat metal pieces their desired three-dimensional form.

What Is Sheet Metal Forming? Sheet metal forming entails taking thin, flat sheets of metal and manipulating them into fully formed 3D structures. The process transforms a basic raw material into complex finished products .The forming of the sheet can be carried out using mechanical tools, with air or with liquids, magnetically or with explosives. Special sheet metal processes include superplastic forming and press hardening, as well as the hot forming . 3.1 Plane Stress and Membrane Stresses. Sheet metal forming processes involve a great deal of plastic deformation; these processes include: bending, deep drawing (with a flat-headed punch), stretch forming, and general sheet forming (Mellor & Parmar, 1978).Most of these sheet forming process, in general, are in the state of plane stress, i.e., the stress, normal to .
sheet metal working process pdf
The main sheet metal forming processes covered are tube bending and forming as well as bending of sheet and plate. Tube bending can be done via press bending, rotary drawing, heat induction, roll bending, and sand packing. Sheet and plate bending includes techniques like roll bending, air bending, bottoming, coining, folding, wiping, and rotary .Incremental sheet forming (ISF) featured with low cost, high customization and small quantity production [19] is achieved through the accumulation of the localized plastic deformation of the sheet, in which a hemispherical-head tool controlled by the computer program is used to form the metal [20].During the forming process, a designed 3D shape is dispersed into levels of 2D .
patina metal sheets
Incremental sheet forming (or ISF, also known as Single Point Forming) is a sheet metal forming technique where a sheet is formed into the final workpiece by a series of small incremental deformations. However, studies have shown that it can be applied to polymer and composite sheets too. Generally, the sheet is formed by a round tipped tool, typically 5 to 20mm in diameter. Metal forming refers to various processes you can use to shape or manipulate materials. Depending on the type of formed part you want, it is vital to adopt a suitable technique. In this article, we will cover 19 different operations you can use to fabricate your metal parts. Let’s dive right in: 1. Rolling Metal [.]
Sheet metal bending is the simplest yet widely used sheet metal forming process. It involves applying a force to a metal sheet to bend it at a certain angle. The material’s thickness, bend angle, and other factors are considered to ensure that the material doesn’t crack at the seams. Components such as brackets, frames, enclosures, etc . 1. Metal forming processes Metal forming: Large set of manufacturing processes in which the material is deformed plastically to take the shape of the die geometry. The tools used for such deformation are called die, punch etc. depending on the type of process. Plastic deformation: Stresses beyond yield strength of the workpiece material is required. Incremental sheet metal forming (ISMF) is commonly regarded as a die-less sheet metal forming process which can form complex three-dimensional parts using relatively simple tools. It is receiving attention from the engineering community due to its flexibility and low cost. This unique combination enables the rapid prototyping of functional .Sheet Metal Forming Process Chain All our software products are aligned with Comprehensive Digital Process Planning, a multidimensional approach which considers function and quality as well as lead time and cost. The appropriate balance of these dimensions has a profound influence on the forming process and results in a new level of .
7. Sheet Metal Forming: It is a process where a sheet of metal is heated and then formed into its desired shape by using a tool or die. This process is often used to create display cases, brackets, and other similar items. Bending is a process where a metal rod or wire is heated so that it becomes soft enough to bend without breaking.
sheet metal stamping process pdf
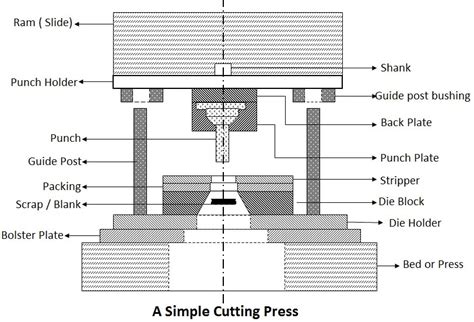
sheet metal processes pdf
A fireplace surround is the metal frame around the fireplace opening. On fireplace inserts , the surrounds hide the gap between the insert and the edge of the fireplace. Masonry fireplaces don't have a gap to cover, but a surround can still be used for decoration.
metal sheet forming process|forming sheet metal by hand