sheet metal fabricating processes The journey from sheet metal to metal products starts with CAD engineering. After making the models, each part goes through the necessary sheet metal fabrication processes. The most common ones are: See more $119.99
0 · types of sheet metal forming
1 · sheet metal manufacturing process
2 · sheet metal forming techniques
3 · sheet metal forming processes
4 · sheet metal assembly techniques
5 · how to form sheet metal
6 · curling process in sheet metal
7 · aluminum sheet metal forming
We manufacture pipe, duct, spiral pipe and fittings, and carry a comprehensive supply of flat sheets, venting, registers and grills, insulation supplies, linesets, and more. Combining expertise and innovation, we deliver top-quality solutions for your HVAC needs, including custom ductwork, precision fittings, and specialized insulation supplies.
The journey from sheet metal to metal products starts with CAD engineering. After making the models, each part goes through the necessary sheet metal fabrication processes. The most common ones are: See moreSheet metal design options are very flexible. Clients can express a need for certain functionality and sheet metal materials leave room for many different solutions. Single . See more
Looking around, it is clear that sheet metal has a plethora of applications. There aren’t many home appliances, constructions, etc. that don’t incorporate . See moreThe manufacturing & design guide. Learn how to effectively design sheet metal parts. This guide starts with the basics and moves toward design best practices and advice on material .The sheet metal fabrication process is an intricate journey from raw metal to a finished product. It involves various steps, ensuring the final product meets specific standards and functions. In .
Sheet metal fabrication is an essential process for many industries, enabling the creation of complex and precise metal components. Understanding the various fabrication techniques is crucial for effective decision-making, cost .The metal fabrication process encompasses manufacturing techniques like bending and cutting, using an array of advanced equipment to produce complex metal shapes, components, and .Sheet metal manufacturing is the process of creating sheet metal parts by cutting, bending, and forming thin metal sheets into specific shapes and sizes. The process typically uses coating, cutting, bending, and assembly techniques.
Sheet metal fabrication is a subtractive manufacturing process that forms parts from thin metal sheets. Engineers often choose sheet metal parts for their high strength-to-weight ratio, durability, and versatility. This guide will . What is Sheet Metal Fabrication? Sheet metal fabrication is the process of forming flat metal sheets into the desired parts and products by cutting, folding, bending, and assembling. Sheet metal fabrication is the process of transforming sheet metal (< 1/4” thick) into finished products, structures, and components. From household appliances to transportation, .
Sheet metal fabrication refers to processes for transforming flat raw metal stock into customized, formed parts with desired shapes and dimensions. It encompasses a variety of techniques, machinery and workflows for bending, .

types of sheet metal forming
Grinding is a finishing process used in sheet metal fabrication to smooth out surfaces, remove burrs and sharp edges, and prepare metal for further finishing treatments like painting or coating. This process involves the use of abrasive wheels or belts that abrade the metal surface to achieve the desired finish. Sheet metal fabrication is a process widely used in modern manufacturing due to its versatility, durability, and cost-effectiveness. It involves shaping and assembling sheet metals into various structures and components . The process of producing sheet metal components using metal sheets is known as sheet metal forming or sheet metal fabrication. This is accomplished by bending, punching, shearing, hydroforming, and other .The sheet metal fabrication process involves design, material selection, cutting, forming, joining, and finishing to create metal components and structures. Conclusion. Sheet metal fabrication is a fundamental process that has shaped the modern world in numerous ways. It is wide ranging, and we have learned that there is no such thing as “the .
Step-by-Step Fabricating Sheet Metal: The following points outline the process undertaken when fabricating sheet metal: 1. Working with Blueprints. In accordance with blueprints generated by the engineer, the sheet metal product specifications will be specified. Rough drawings will be made to understand the scope of the sheet metal fabrication . Industrial metal fabrication is the driving force behind creating the durable, high-quality products that keep industries moving forward. Picture the towering steel frameworks of buildings, the precise components in machinery, and the metal products the world relies on daily—none of it would be possible without these intricate fabrication processes.
The term “sheet metal fabrication” describes the process of transforming flat metal sheets into metal products and structural designs. Most sheet metal processing techniques include converting various sheet metal types into components and parts by employing precision equipment like a CNC machine and several forming methods.
Sheet metal forming is a sheet metal fabrication process that manipulates metal into flat sheets into complex shapes. Employed extensively across various industries, this technique involves a range of operations such as bending, drawing, and punching. Through methods like stamping and laser cutting, manufacturers can produce parts with precise . Sheet metal fabrication is a complex manufacturing process that includes cutting, bending, hole punching, embossing, and many other forming operations. As the parts have more features, the complexity of the design also increases. Therefore, you must consider the sheet metal design guidelines to ensure manufacturability. Common Tolerancing Problems in Metal Fabrication. We frequently receive RFQs for parts with tolerances that exceed what is achievable in standard fabrication. Most of these issues are related to sheet metal forming, such as achieving ±0.005 tolerance across multiple bends, which surpasses our recommended default sheet metal tolerances.Additionally, we . Sheet metal fabrication is the process of transforming sheet metal (< 1/4” thick) into finished products, structures, and components. From household appliances to transportation, commercial equipment to construction, sheet metal fabrication is critical to modern manufacturing. In this article, we cover the basics of sheet metal fabrication, from material selection to key .
Sheet metal forming is a sheet metal fabrication process that manipulates metal into flat sheets into complex shapes. Employed extensively across various industries, this technique involves a range of operations such as bending, drawing, and punching. Through methods like stamping and laser cutting, manufacturers can produce parts with precise .The final step of the sheet metal custom fabrication process involves treating a part’s surface, smoothing out rough edges and burrs and removing surface flaws through processes like deburring. Finishing treatments and secondary services help provide surfaces with added resistance to corrosion and an aesthetically pleasing appearance. Surface .Discover the essentials of Bend Allowance in sheet metal fabrication - your key to precise, high-quality metalwork projects! Bend compensation refers to the adjustments made during the bending process of sheet metal to account for the material's stretching and compression. It involves the understanding that, during bending, the length on the .Sheet metal bending is a common and essential process in a sheet metal fabrication factory. This technique is the plastic deformation of a piece of metal along an axis, resulting in a change in the part’s geometry. Like other metal .
The sheet metal fabrication process paved the way for the innovative design of automobiles due to the availability of production-grade materials. The metal-forming capabilities of this technology help create perfect frames from thin metal sheets. Hence, most car parts undergo punching and laser operations. For example, most vehicles’ hoods . Because the metal fabrication business has applications in nearly every industry, there are many different processes and techniques that are used to create an endless variety of products. The floor of a metal fabrication shop .
The three main types of sheet metal fabrication processes, each with its unique methods, applications, and advantages are: Cutting. Cutting is the first step in the sheet metal fabrication process. It involves separating the sheet metal into desired shapes and sizes. Common cutting methods include shearing, laser cutting, plasma cutting, and . Metal fabrication, transforming raw metal into finished products, has evolved remarkably. What once relied heavily on manual labour and traditional techniques such as metal flattening, bending, and forming has been revolutionised by mechanical automation in modern metal fabrication workshops. Wrightform take a quick look into the journey of metal fabrication, . Discover the various processes of sheet metal fabrication. From cutting and bending to finishing and assembly, explore over 50 techniques and boost your knowledge. 1. Rolling Metal. In the fabrication sector, rolling metal is among the most often used techniques. This procedure will be helpful particularly when dealing with sheet metal. Rolling reduces thickness by passing metal stock between two rollers, therefore guaranteeing consistency and strength. Large-scale projects like manufacturing steel beams .
The sheet metal fabrication process consists of multiple steps to safely produce reliable products. Although specific steps may vary slightly, the overall process is the same. Step #1: Generate Blueprints. Products or pieces of equipment made from sheet metal first begin as a blueprint or plan. The engineer working on the project is responsible .Unless a sheet metal does not need to be cut to size, most fabrication processes start off with blanking, or cutting a smaller piece of metal workpiece from a larger sheet or plate. For stamping, this is followed by placing the workpiece into a press machine which contains different tooling dies to achieve a specific design.
The Importance of Understanding Sheet Metal Fabrication Techniques. Sheet metal fabrication is an essential process for many industries, enabling the creation of complex and precise metal components. Understanding the various fabrication techniques is crucial for effective decision-making, cost optimization, and quality control. The significance of sheet metal fabrication extends across various industries, from automobile and construction to aerospace and energy. Essentially, What is sheet metal fabrication? It is the technique of sheet metal cutting, bending, and assembling metal to form parts and structures for diverse applications. This process is fundamental in creating both functional . Metal fabrication is a process that is a big part of a lot of products and appliances that regular people use in their day-to-day life. This article attempts to present some basic information about metal fabrication, its different types, methods and so on. . Different stages of the sheet metal fabrication process. Benefits Of Sheet Metal Fabrication. Sheet metal fabrication is shaping metal using various tools and machines. Versatility. It can create various products, from car parts to kitchen appliances. Speed. Sheet metal fabrication is a relatively fast process, which can be completed in hours or days. Precision.
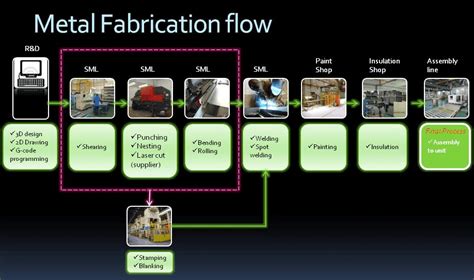
sheet metal manufacturing process
Whitehall™ Personalized Cast Metal Address plaque with oval shape. Made in the USA. BEWARE OF IMPORT IMITATIONS. Four colors, four shapes .
sheet metal fabricating processes|types of sheet metal forming