sheet metal welding techniques Each welding process requires specific precautions and equipment setup for a successful sheet metal weld. So, let’s discuss the preparation needed for each arc welding process before proceeding to the common problems with thin gauge welds. See more Metal fabrication is the processing of metals to create various metal objects. The process of metal fabrication can happen in one step or can even take tens of steps, depending on what is required.
0 · welding thin metal with stick
1 · welding sheet metal with mig
2 · welding 24 gauge sheet metal
3 · welding 22 gauge sheet metal
4 · welding 16 gauge sheet metal
5 · welder settings for sheet metal
6 · mig welding sheet metal basics
7 · best welder for sheet metal
File Form 1099-R for each person to whom you have made a designated distribution or are treated as having made a distribution of $10 or more from: Profit-sharing or retirement plans. Any individual retirement arrangements (IRAs). Annuities, pensions, insurance contracts, survivor income benefit plans.
Each welding process requires specific precautions and equipment setup for a successful sheet metal weld. So, let’s discuss the preparation needed for each arc welding process before proceeding to the common problems with thin gauge welds. See more
Now that we’ve covered the essential considerations for different arc welding processes, let’s discuss how to prevent and fix common . See moreWelding thin metal is challenging. There is no denying that. But, if you practice and use the tips we shared in this article, you’ll get the best chance for success. After you inevitably burn through some scrap sheets of metal and warp others, you’ll gain more experience and learn . See more
Preventing burn-through and warping when welding sheet metal is all about controlling the heat. Choose the right welding process and filler metal, and follow these . Sheet metal welding tips. Of course, there are other variations when it comes to welding of sheet metal that can be somewhat less known and suitable for specific use cases. This list went over the majority of popular sheet .
Welding sheet metal is a very critical process within the modern concept of manufacturing. The construction of metal structures, pipelines, and tanks is among the most common applications for sheet metal welding. . Sheet Metal Welding Tips. To achieve high-quality welds in sheet metal fabrication, consider the following tips. Whether you are .Mastering TIG Welding Techniques for Sheet Metal. TIG welding sheet metal demands precision and skill. Let’s explore the techniques that will elevate your welding game. Key Principles of TIG Welding Sheet Metal. Success in TIG . The best way to simplify this welding surface is to minimize the weld puddle and use enough filler metal. Expert Tips For Sheet Metal Welding. Beyond understanding different methods of welding sheet metal, including the best metal for your fabrication, achieving optimal results requires precision and skills. The following are expert tips to . At Approved Sheet Metal, we find that welding sheet metal is one of the most misunderstood processes in precision sheet metal fabrication. In an effort to demystify welding and help our customers choose the optimal welding method for a part, we do our best to clearly outline the benefits and limitations of different custom welding techniques.
Gas welding, also known as Oxy-fuel welding, is a traditional method of sheet metal welding that utilizes a flame to heat and melt the metal, which is then fused together by a filler metal. While it may not be as widely used as other modern welding techniques, it remains a popular choice for certain applications such as repair and maintenance .
Sheet metal welding is a multifaceted craft that requires applying numerous techniques. Acquiring the requisite knowledge and skills is imperative to perform welding with optimal outcomes. This article examines the diverse techniques employed in welding sheet metal materials , including their merits and practical uses. Sheet metal welding is a crucial process in various industries where joining thin metal sheets is necessary to fabricate structures, components, and assemblies. This welding method plays a vital role in industries such as automotive, aerospace, construction, and manufacturing. So, You never want to go wrong with sheet metal welding. Read this article, . Essential Tips on How to Weld Auto Body Sheet Metal Use the skip welding technique. Using a skip welding technique will help prevent heat build-up and warping. Skip welding consists of laying a series of tack welds about an inch apart and joining them together in a different order instead of one long bead. These short welds at different points .
Expert Tips for Welding Sheet Metal. When welding sheet metal with MIG or TIG, achieving precision and control is crucial to avoid warping and distortion. The following tips will guide you through the important aspects of welding techniques and material choices to ensure high-quality results. Select the Right Filler Metals
Sheet metal welding is therefore a crucial component of metal fabrication. Do you know which sheet metal welding technique is best for your industrial applications out of the various available techniques? This article offers a thorough overview of the many sheet metal welding techniques, along with an analysis of their benefits and uses. Mastering the art of stick welding sheet metal can be a game-changer for both seasoned professionals and DIY enthusiasts. With its enduring appeal and robust results, stick welding brings a sense of craftsmanship to metalworking like no other. In this comprehensive guide, we delve into the nuanced techniques and best practices that elevate your sheet metal . MIG Welding Sheet Metal Tips. To enhance your proficiency in MIG welding sheet metal, incorporating certain tips and techniques can significantly impact the overall quality of your welds. Utilizing a smaller diameter welding wire, such as 0.023 inches, offers better control and precision when working with thin sheet metals. . Welding positions Bonus Tips for Sheet Metal Welding. Several tips should be acknowledged during welding to improve the quality to meet the highest standard welds. Use the proper filler metal: The filler metal should have corrosion resistance, excellent joint strength, and be .
In this video I demonstrate how to set up your mig welder so you can weld thin sheet metal. We also showed in this video how to make your pattern, fit and we. Understanding sheet metal fabrication techniques can empower you to make informed choices for your organization. 314-994-9550. Home; Our Services. Metal Fabrication. Laser Cutting; Turret & Punch; Forming; Weld & . In manufacturing, sheet metal parts must be joined to form a final product called assembly. Metal welding is a prominent assembly technique. Different types of welding play a crucial role in permanently joining individual .
electric tiffin box price in pakistan
Burn-through and blowholes are common issues in sheet metal welding. Techniques like using a lower heat setting, adjusting travel speed, and choosing a suitable filler material can help avoid these problems. Rectifying Uneven Welds. Uneven welds can lead to weak joints. You may need to adjust your welding technique, travel speed, or even the . Some common welding techniques for sheet metal include resistance spot welding, gas metal arc welding, and laser welding. Adhesive bonding is a technique that employs special adhesives to bond the sheet metals. This method is advantageous for joining dissimilar materials and relatively thin sheets. Adhesive bonds also offer a smooth, aesthetic . Utilize filler metals (wires) that are slimmer as compared to reedy sheet metal. Numerous welders utilize 0.023-inch diameter wires and 0.024 inches for slimmer sheet metals. 18-gauge metals such as stainless steel have wire diameters of 0.030 and 0.034 inches. . (Shielded Metal Arc Welding). This welding technique is older as compared to . Stick welding, also called Shielded Metal Arc Welding (SMAW), is a flexible sheet metal welding technique using a consumable electrode with a flux coating. As the electrode melts, the flux makes a protective slag over the weld, shielding it from air contamination.
We conduct welding sheet metal assembly by fusing two pieces to form a single product. Usually, we use welding sheet metal assembly when you need strong and permanent structures. . Some of the welding techniques which you can use include the following: Spot weld assembly: in case you require structures that are not permanent, we advise you to .Sheet metal welding is a welding process used to join thin metal sheets, usually involving metal materials with a thickness of 1/16 inch (about 1.5 mm) to 1/4 inch (about 6 mm). The process is commonly used for different types of metals, such as aluminum, stainless steel, and carbon steel, and is widely used in manufacturing, construction . 3 Expert Weldment Techniques at Approved Sheet Metal. . Approved Sheet Metal’s welding team is trained to the highest standards. Our best practices include: Using only low heat to avoid metal distortion. When too much heat is applied to a part during welding, it can curve, oil-can, or warp. Only an experienced team like ours has the know .
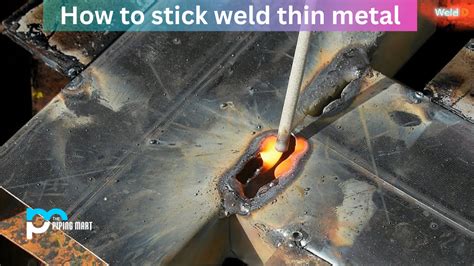
What is Metal Sheet Welding? Metal sheet welding refers to the process of joining two or more metal sheets into a single unit through heating or pressure, creating atomic bonds between them. This process is widely used in CNC machining part manufacturing, especially in industries like automotive, aerospace, construction, and electronics. 6 .I have over ten years of professional experience in sheet metal fabrication, specializing in laser cutting, bending, welding, and surface treatment techniques. As the Technical Director at Shengen, I am committed to solving complex manufacturing challenges and driving innovation and quality in each project. Employ a pulsing technique, stitch welding, or tack welds to manage heat and allow cooling periods between welds to minimize warping. . Ensure you use very thin wires when working with reedy, thin sheet metal. Metal Thickness (inches) Recommended MIG Wire Size (inches) 0.024: 0.020: 0.030: 0.023: 0.036: 0.025: 0.048: 0.030: 0.060:
welding thin metal with stick
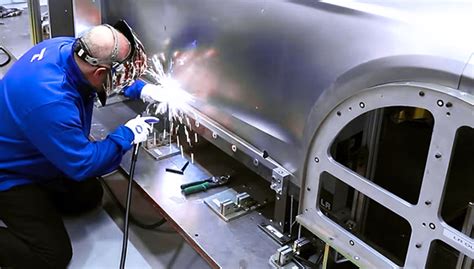
A nondividend distribution is a distribution that's not paid out of the earnings and profits of a corporation. Any nondividend distribution is not taxable until the basis of the stock is .
sheet metal welding techniques|welding 24 gauge sheet metal