tool monitoring on cnc machines Caron Engineering's TMAC tool monitoring system for CNC machining optimizes tool cutting with high-precision sensors, a dedicated high-speed data processor, and an intuitive human . We tested top-rated options to help you find the best lunch boxes for whatever type of meal you plan to pack. This lunch box earned our best overall spot because it's a nice, .
0 · real time production monitoring
1 · real time machine monitoring
2 · machine run time tracking
3 · machine monitoring system for manufacturing
4 · equipment monitoring system dashboard
5 · cnc machine monitoring systems
6 · cnc machine data collection
7 · best cnc machine monitoring software
$30.99
Tool monitoring leverages data from CNC machines to understand and predict the condition and lifecycle of the tool, reducing tooling and scrap part costs.
MachineMetrics Tool Monitoring captures machine data straight from Fanuc .
MachineMetrics Tool Monitoring captures machine data straight from the machine .Caron Engineering's TMAC tool monitoring system for CNC machining optimizes tool cutting with high-precision sensors, a dedicated high-speed data processor, and an intuitive human .Maintain Tools and Machine: Regular maintenance of both tools and the CNC machine is essential for optimal performance. Dull or damaged tools can increase spindle load, while neglected machines are more prone to errors and malfunctions. . Example of Spindle Load Monitoring. Consider a CNC shop machining steel components using a 3-axis mill .As one of the core equipment of intelligent manufacturing, the condition monitoring of CNC machine tool is the key of intelligent manufacturing. In this paper, the heterogeneous data standardization specification is implemented by establishing an expandable CNC machine tool description model, the CNC machine tool monitoring system based on OPC Unified .
real time production monitoring
System for Tool-Wear Condition Monitoring in CNC Machines under Variations of Cutting Parameter Based on Fusion Stray Flux-Current Processing . Antonino-Daviu J.A., Trejo-Hernandez M., Osornio-Rios R.A.A. Cutting Tool Wear Monitoring in CNC Machines Based in Spindle-Motor Stray Flux Signals. IEEE Trans. Ind. Inform. 2020:1. doi: 10.1109/TII .
Machine tools, critical for manufacturing industries, need maintenance for performance and profitability. . CNC machine monitoring involves real-time tracking and analysis of machine performance metrics such as spindle speed, tool wear, and production output to optimize efficiency, detect anomalies, and schedule maintenance proactively.Modern CNC machine monitoring systems collect real-time data from machines, providing insights into various performance metrics such as spindle speed, feed rate, tool usage, and machine status. This data is analyzed to detect anomalies, predict maintenance needs, and optimize machine parameters, ensuring consistent and high-quality output.
Complete systems for tool monitoring and process control for all types of metal cutting machine tools. Control-integrated tool monitoring for open CNC control panels; Sensors for monitoring micro tools; Integrated acoustic work piece dimension control . Tool wear monitoring and real-time predicting tool life during the machining process is becoming a crucial element in modern manufacturing to properly determine the ideal point to replace tool, remains a challenge currently. In this paper, the model approach for in-process monitoring and predicting progressive tool wear by using machine vision is proposed. .
real time machine monitoring
In CNC machining, the cutting tool’s integrity is vitally necessary since tool wear heavily affects workpiece quality, production efficiency, machine stability, and durability of the cutting process. . and machine learning algorithms are utilized to perform tool condition monitoring and machining control. The ultimate goal of this research .
Caddis can be installed onto any type of CNC machine within minutes with either a stack-light, Wi-Fi, cellular or ethernet model to provide you with critical real-time manufacturing analytics related to uptime, preventative maintenance, utilization, excessive downtime, temperature and vibration.CNC Machine operators can easily access this data from any type of device and .2.2 Assembly of Toolholder On-Rotor Sensing. To maintain the original milling machine tool handle structure and not weaken its strength, the sensing unit is installed on the cutter arbor shown in Fig. 1.At the same time, to reduce the influence of static centrifugal force generated by spindle rotation, an inner ring with an inclined plane is designed in this scheme, as shown in .Detect broken tools, check for part removal and more with a tool breakage detection system (Positive contact sensor). Tool breakage detection and monitoring systems can save companies huge costs in many areas including scrap parts, downtime, setup time, part inspection as well as repair and maintenance costs from crashes which could have been avoided with a positive . The computer numerical control (CNC) machine has recently taken a fundamental role in the manufacturing industry, which is essential for the economic development of many countries.
machine run time tracking
Machine tool monitoring is explained with Acoustic Emission (AE) sensors. [7] An AE sensor is commonly defined as the sound emitted as an elastic wave by a solid when it is deformed or struck, caused by the rapid release of localized stress energy.Therefore, it is an occurrence phenomenon which releases elastic energy into the material, which then propagates as an . In this section, we provide an overview of the existing research and developments in the field of vibration monitoring for CNC machines. Vibration monitoring plays a pivotal role in ensuring the accuracy, reliability, and efficiency of CNC machining processes. Chatter affects the product quality significantly [9,10].
Detect broken tools, check for part removal and more with a tool breakage detection system (Positive contact sensor). Tool breakage detection and monitoring systems can save companies huge costs in many areas including . Tool wear and breakage detection is one of the most important problems found during manufacture in automated CNC machines. From several techniques devoted to sense tool condition, driver current monitoring has been used for a sensorless approach.
Complete systems for tool monitoring and process control for all types of metal cutting machine tools. Control-integrated tool monitoring for open CNC control panels; Sensors for monitoring micro tools; Integrated acoustic work piece dimension control .
Tool wear, tool failure, and tool life are a reality of cnc machining. All tools experience tool wear and will eventually fail if they continue to do work. . Data can be collected to monitor the machine tool and develop thresholds for when tool failure is imminent. Using thresholds to determine when a tool is reaching end of life so that it .Tool condition monitoring (TCM) is one of the most relevant tasks during a machining process. The latest high-quality productivity standards make it essential to monitor the cutting tool wearing. Current TCM methodologies demand the installation of sensors near the working area, which in practical terms, it is not the most optimal solution since the final diagnosis can be disturbed by .Most CNC machining shops now have operators running more than one machine at a time. If the operator is not in the area when the tool life alarm goes off, the machine sits there idle, which cuts into your profit margin. . Monitor re-ground tool lengths. (2, 3) Reset tool wear compensations values. Output information on tooling to a file on . Computer Numerical Control (CNC) machines are crucial in producing high-quality parts in the manufacturing industry. The wide range of tools and operations involved in CNC machining, including variations in shape, geometries, materials, coatings, and physical changes, pose significant challenges [1], [2].Moreover, the complexity is amplified by variations in .
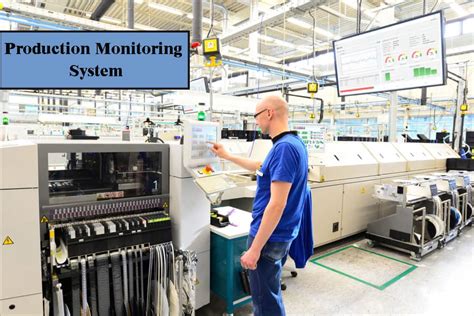
FANUC MT-LINKi Machine Tool Monitoring Software. FANUC MT-LINKi and FANUC MT-LINKi Integration Server are fully scalable, out-of-the-box machine tool monitoring solutions that can monitor and manage data from one to two thousand machines. Operational and production data is monitored and collected using a PC and an Ethernet connection. A variety of data points are .Machine tool monitoring systems gather information from the main CNC machine, before then processing everything and interpreting the data. With the information gathered, it is possible to determine where any weaknesses and failures are in the overall production process. Machine tools play an important role in the global economy. Wang et al. [1] explored 27 major countries involved in metal cutting processes that form the machine- tool industry and cover 95% of the total production. . Lastly, the acceleration of vibration signals was plotted to monitor four CNC machines in real time using IoT. Fig. 5 RMS . Navigating Large-Scale CNC Machining: Suburban Tool’s Niche Strategy to Stay Competitive Facing increasing competition from lower-cost imports, Suburban Tool made a move toward large-scale, in-house machining. . Tips for Monitoring Spindle Loads and Cutting Stability. When it comes to utilizing the spindle’s power, there is a lot of .
machine monitoring system for manufacturing

Why Monitor Tooling on a FANUC? Tools used in CNC machining are costly. The harder the material and more complex the jobs, the more costly the tools are. Tool life monitoring is essential because it allows companies to maximize their tools' ROI. Automated machine tool monitoring offers many benefits that impact efficiency and cost. These include:The first machine, M/c1, is a semi-production CNC milling machine (HAAS, Mini Mill) having axes travel of 406 × 305 × 254 mm and a maximum spindle speed of 6,000 rpm. The second machine, M/c2, is a CNC vertical machining center (MAZAK, Variaxis 630-5X II T) having axes travel of 630 × 760 × 600 mm and a maximum spindle speed of 18,000 rpm.
equipment monitoring system dashboard
cnc machine monitoring systems
$151.12
tool monitoring on cnc machines|cnc machine data collection