what is air bending sheet metal To create a bend, the press pushes the top tool downwards a set distance, bending . Two junction boxes are each located on different walls, 18'' from the same corner. Given a 90 ° bend with a take-up of 6 ° and a gain of 4", what is the developed length of the conduit between the junction boxes? 26 ° 32'prime 36 ° 46 °
0 · sheet metal curve bender
1 · sheet metal brake bending angle
2 · sheet metal bending force formula
3 · is air bending possible
4 · air bending vs bottom coining
5 · air bending vs bottom
6 · air bending dies
7 · air bending bottoming and coining
Install the ground wire into a metal junction box. Connecting all the wires leaves you with one loose wire. This wire should be either green or copper-colored. Locate the ground screw inside the junction box, which must be machine threaded and green in color.
Air bending and bottom bending are two of the most common methods used to create bends during sheet metal fabrication. The names given to each method may sound unusual at first, but as you’ll see, both names actually describe each bending process perfectly.

stainless steel shower enclosure manufacturer
To create a bend, the press pushes the top tool downwards a set distance, bending .To create a bend, the press pushes the top tool downwards a set distance, bending the material inwards into the the v-shaped bottom tool. Air bending is called air bending because a gap is . Air bending (also known as free bending) is the most common way for bending sheet metal because of its flexibility. In air bending, a bend angle .

sheet metal curve bender
Air bending is the most common type of 3 Types Of Bending used in sheet metal shops today. In this process the workpiece comes in contact with the outside edges of the die, as well as the punch tip. Partial bending, or air bending, derives its name from the fact that the working piece does not actually touch the tooling parts entirely. In partial bending, the workpiece rests on 2 points and the punch pushes the bend.
Air bending harnesses the force of compressed air to manipulate sheet metal with precision. Unlike traditional roll bending, which uses rigid rollers to deform the metal, air . Nonetheless, for almost 60 years they were the most common way to bend metal—until the industry took the next leap forward with air forming. So, what exactly is air forming (or air bending) , and how does it work compared to .Air bending is a method of forming sheet metal using a punch and die. In a part produced using air bending, the metal is placed between a punch and a V-die as shown below: As the press brake forces the punch and the die together, the . Air bending is a sheet metal fabrication technique where a punch and die are used to bend without forcing the sheet to follow the die shape. Placing the metal sheet on a V die and punching it. The depth of the punch .
sheet metal brake bending angle
sheet metal bending force formula
Figure 1-18 Z-shaped step bending. VI. Bending by Press Brake Machine. There are two categories of bending machines: ordinary bending machines and CNC bending machines. CNC bending machines are typically .
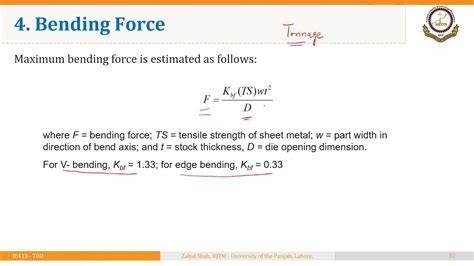
During large-radius bending sheet metal yields less than during other types of bending, so springback is greater and difficult to calculate. . Features of air bending: Wide bending angle with one set of tooling. The angle .
Air bending is one of the most widely used metal sheet bending processes, especially as it doesn’t require high levels of force. Bottom Bending Again, as with air bending with bottom bending, the punch and the die don’t .
Factors influencing the K-factor include material properties (such as yield strength and ductility), sheet thickness, bend radius, and bending method (air bending, bottoming, coining). Modern sheet metal fabrication often utilizes empirically derived K-factor tables or advanced finite element analysis (FEA) to determine optimal values for . In doing this, a press brake tool is usually employed to bend the sheet metal. Types of Metal Bending. There are three basic types of metal bending: Air bending, Bottom Bending/Bottoming, and Coining. These typifications are based on the relationship of the end tool’s position to the thickness of the material. Air bending The difference between these two processes is that coining uses up to 30 times more pressure to bend sheet metal than air bending, making it highly useful for bending thick and/or hard sheet metal. Bottoming. Bottoming is a bending process in which sheet metal is pressed against a bottom die featuring a V shape. While other bending processes .Air bending.Image credit: https://www.rapiddirect.com Air bending is a widely-used sheet metal bending technique that involves positioning the sheet metal on a die, with the bend line aligned over the die’s apex. A punch is then applied to the material, forcing it to bend around the die’s profile. One of the key advantages of air bending is its versatility, as it allows for multiple bend .
The sheet metal bending process commonly involves three bending basics methods: air bending and bottom bending, as well as coining. In this passage, we will focus on the press brake air bending. We will introduce the definition of air bending, its importance, process, and so on, to help readers better understand and apply this sheet metal .Air bending is a method of forming sheet metal using a punch and die. In a part produced using air bending, the metal is placed between a punch and a V-die as shown below: As the press brake forces the punch and the die together, the metal folds where the .
Air bending is known as air bending because the sheet metal is not fully pressed into the die during bending. Instead, as in the image above, air is left between the sheet metal and the die. With air bending there are always only three contact points during bending: One on each side of the top of the V opening of the die and one at the tip of . Top Vs. Bottom Bending. Air and bottom bending are two of the most dominant sheet metal forming methods. Air bending consists of stressing the sheet past an open die until the die angle is reached, and this shape depends on how much stress is .
Bottom Bending. The difference between air bending and bottom bending is that there is a difference in radius between the two. It differs from coining as the punch and the tie don’t make full contact with the material, and there isn’t enough tonnage to make an imprint into the metal.https://sendcutsend.com/Send Cut Send - Online Laser Cutting, Waterjet Cutting and CNC Router ServiceIn this video: The first video in a new series on bendin. V-bending is the most common bending method using a punch and die. It has three subgroups – bottoming, air bending and coining. Air bending and bottoming account for around 90% of all bending jobs. The bending force table below helps you identify the minimum flange length b (mm) and inside radii ir (mm) according to material thickness t (mm).
FAQs About Air Bending Force Chart How to Read the Air Bending Force Chart? You can get the following information from the air bending force chart above if the data of the metal thickness and bending inner raidus are .
is air bending possible
In sheet metal forming, the bending moment determines the stress distribution across the sheet and the material’s behavior under load. When applied to sheet metal, the bending moment increases with the length of the . Air bending is probably the most widespread method of sheet metal bending. Its working principle is forcing a workpiece’s surface into a V, U, or any other shape. It is done simply by punching metal with a strong, working tool. .Air Bending. Air Bending is the most common type of bending process used in sheet metal shops today. In this process the work piece is only in contact with the edge of the Die and the tip of the Punch. The punch is them forced past the top of the die into the v-opening without coming into contact with the bottom of the v. The v opening is . 5. Sheet Metal Bending Collisions. Whether it’s an asteroid, a motor vehicle, or a sheet metal part, collisions really aren’t a good thing. In the world of bending, a collision occurs when the material to be bent contacts any surface other than the dies.
Bottom bending also works with a sharp punch bend radius. But a sharp punch radius in air forming only creates problems, which is probably the main reason some shops and operators fail to make the transition from coining and bottom bending to air forming. A sharp bend is defined as any tool radius less than 63 percent of the material thickness.
Figure 1 In air bending, a sheet is placed in the die, and the press ram descends and bends the sheet into a V shape.: Figure 2 Bend allowance (also known as bend deduction) can be used to predict the initial flat length of the sheet. Source: O. Diegel, "Bend Works: The Fine Art of Sheet Metal Bending," Complete Design Service, 2002. Figure 3 Bend allowance .I know the advantages as zero springback and smallest possible radius. And we also making articles in bending. But we have and make a lot of warnings in air bending because people try to find the way to bend harder than for press brake as possible and with coining with 6-8 times more tonnage - it is impossible. The smallest inside radius that can be achieved by air bending sheet metal is .63 x material thickness. Maximum punch radius ≤ the natural radius of the bend. When is the punch tip radius too large? When planning to air bend a part, the best practice in developing the blank size is to use the naturally formed inside radius of the bend to .
Dialing in the k-factor for bending sheet metal parts The k-factor matters, but metal fabricators shouldn't overlook the tooling and bending method. By Steve Benson; November 20, 2023 . hence, this 120-KSI sheet will air-form a radius that’s about double that of cold-rolled steel—or 32% of the die opening (16% × 2). Back to the BA, the . The type of sheet metal bending that is used depends on the desired outcome and the type of sheet metal being used. There are three main types of sheet metal bending: Air bending: This is the most common type of sheet metal bending because it is fast and easy to do. It is a process that uses a punch and die to bend sheet metal.An Air Bend Force Chart, or Force Chart breaks down a number of key components of sheet metal bending in an easy to reference format. Being able to read a bend force chart is crucial for any Brake Press operator and sheet metal engineer. The gauge, inside radius, die opening, and minimum flange length are all interconnected through different equations and relationships, the .Air Bending is a fascinating technique that falls under the umbrella of metal bending. Unlike other methods that rely on direct contact with the metal to create a bend, air bending introduces a unique approach. . One of the key factors to consider when bending sheet metal is its malleability. Malleability refers to the metal’s ability to be .
air bending vs bottom coining
PV junction box with MC4 compliant connectors. When purchasing solar modules, always have a look at the IP rating of the PV junction box. A completely water tight junction box carries IP 67. IP65 rated PV junction box. How does the PV junction box protect the solar panel? Most photovoltaic junction boxes have diodes. The function of the diodes .
what is air bending sheet metal|air bending dies